Inflatable paint booths have become an increasingly popular option for auto body shops, small repair businesses, and even hobbyists looking to paint vehicles or other equipment. These temporary structures made of vinyl materials allow for spray painting operations almost anywhere while containing overspray and fumes. However, questions around the legality of inflatable paint booths have emerged as their use has grown.
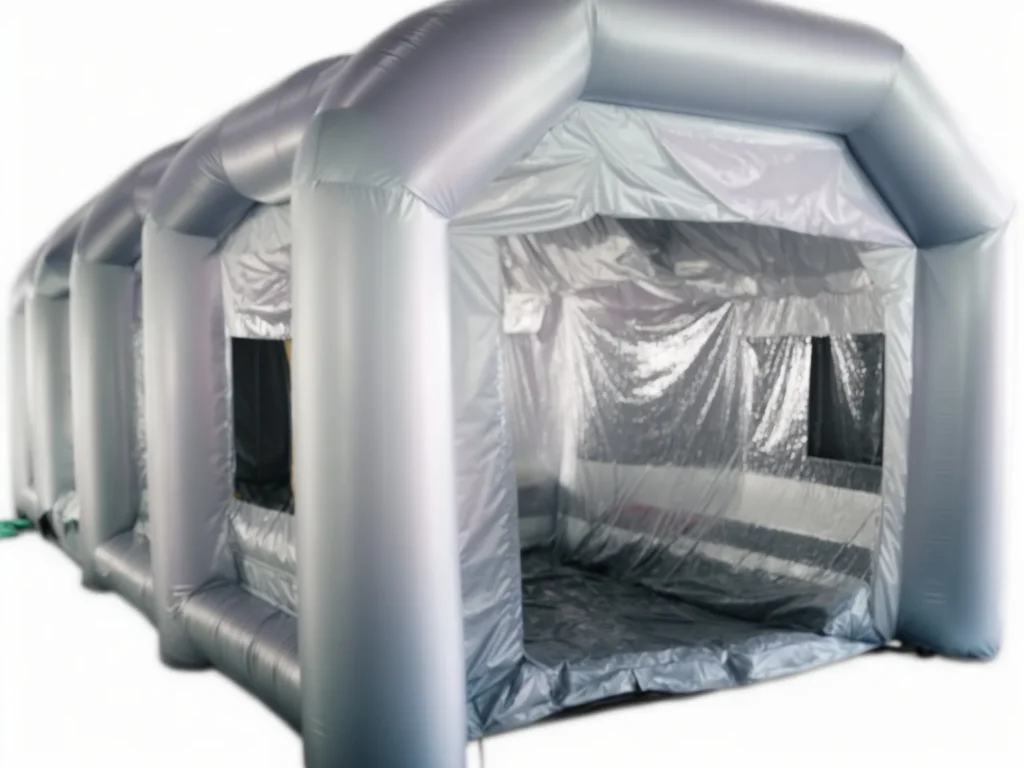
Overview of Inflatable Paint Booth Structures
Inflatable paint booths are designed as portable, temporary enclosures that can be set up when needed for painting operations and then taken down and stored away afterward. Here are some key features of typical inflatable paint booth structures:
- Made of fire-retardant vinyl materials that are durable and easy to clean. The inflatable chambers are often supported by aluminum or steel frames.
- Include built-in exhaust ventilation ports or tubes to connect to exhaust fans and filtration systems.
- Flooring made of thick plastic tarps to catch overspray drips and spills. The floors are disposable or reusable.
- Can be paired with lighting systems, spray gun mounts, airsupply hoses, and other equipment.
- Available in various sizes from small 9ft x 12ft hobbyist booths up to large commercial units.
- Designed for quick assembly and breakdown, not requiring permanent construction.
- Offer affordable painting enclosures vs fixed spray booth installation. Inflatable booth prices from $500 to $5000.
Key Benefits:
- Portability – Can be used anywhere needed and moved between sites. Great for mobile auto detailing businesses.
- Fast Setup – Inflatable booths can be operational in under an hour.
- Low Cost – More budget friendly options compared to permanent spray booth construction.
- Temporary Use – Short term painting needs for a few weeks or months.
- Flexible Size – Suitable for small car repairs up to large commercial jobs.
- Contained Overspray – Catches paint overspray and fumes.
Are Inflatable Paint Booths OSHA and NFPA Compliant?
While inflatable paint booths offer significant advantages for portability and fast setup, questions come up around whether they meet legal requirements for worker safety and fire code compliance. The two key organizations that regulate paint booth equipment are OSHA and NFPA:
- OSHA – The Occupational Safety and Health Administration sets legal standards for equipment like ventilation, fire suppression, and electrical systems.
- NFPA – The National Fire Protection Association provides codes and standards around fire safety of structures and materials.
To be compliant and legally approved for use, inflatable paint booths must meet the criteria set forth in the following key OSHA and NFPA codes:
OSHA Standards
- 29 CFR 1910.107 – Spray Finishing Operations – Defines safety rules for ventilation, airflow, fire prevention, and electrical wiring.
- 29 CFR 1926.102 – Flammable Liquids – Classifies paint materials and required handling.
- 29 CFR 1910.134 – Respiratory Protection – Requires use of proper masks or respirators when spraying hazardous paint materials.
NFPA Code Standards
- NFPA 33 – Spray Application Using Flammable or Combustible Materials – Provides fire code rules around paint booth construction, ventilation, and fire suppression.
- NFPA 70 – National Electrical Code – Sets electrical safety standards that paint booth systems must meet.
- NFPA 33 1 – Building Construction Code for Paint Booths – Defines construction specifications and approved materials.
So in summary, inflatable paint booths must comply with OSHA standards for worker health and safety as well as NFPA codes for fire prevention in order to be considered legal for use.
Typical Requirements for OSHA and NFPA Compliance
Here are some of the key requirements inflatable paint booths must meet to comply with national OSHA and NFPA standards:
- Fire-retardant Materials – All inflatable booth fabrics and panels should meet NFPA fire code standards for flame resistance. Vinyl materials should not readily ignite.
- Grounding Wires – Proper grounding of metal booth components and prevention of static buildup is crucial. All wiring must meet National Electrical Code safety rules.
- Exhaust Ventilation – Adequate exhaust fans and ducting must be in place to meet OSHA ventilation velocity and air turnover standards. This prevents buildup of flammable fumes.
- Air Supply Filters – Fresh air make-up systems should have filtration to remove overspray particles from intake air to prevent ignition hazards.
- Fire Suppression – NFPA 33 mandates fire extinguishers or sprinkler systems nearby.
- No Ignition Sources – Electrical systems, lighting, and other potential spark sources must meet fire prevention codes.
- Distance from Workers – OSHA requires sprayers maintain at least 3 feet distance from other workers during painting. Booth size must accommodate this.
- Overspray Collection – Floors must fully catch and contain all overspray drips and residue according to OSHA guidelines.
- Permissible Exposure Limits – Ventilation must keep hazardous paint fumes below OSHA’s legal limits for worker exposure.
Proper documentation and testing is crucial to prove compliance. Reputable inflatable booth suppliers can provide documentation showing their systems meet both OSHA and NFPA standards.
Are Inflatable Paint Booths Allowed for Automotive Refinishing?
A common use case for inflatable paint booths is for auto body shops, mobile detailers, and auto enthusiasts painting vehicles or vehicle components like bumpers, wheels, etc.
The key question is whether inflatable paint booths meet regulations for automotive refinishing. The Environmental Protection Agency sets guidelines for this industry in their 40 CFR 63 Subpart HHHHHH regulations referred to as 6H rules.
The 6H rules define maximum levels of volatile organic compounds (VOCs) and hazardous air pollutants (HAPs) that can be released by automotive paint facilities. This requires proper filtration on booth exhaust systems.
Inflatable paint booths can comply with 6H regulations when set up with the necessary exhaust filters to meet VOC and HAP emission limits. Appropriate filters like dry filters, water wash filters, or carbon absorption systems allow inflatable booths to qualify for legal automotive painting use.
Documentation and recordkeeping on filter efficiency is important to prove 6H compliance during any regulatory inspections.
Local Ordinances on Inflatable Paint Booths
While federal OSHA, NFPA, and EPA regulations provide standards inflatable paint booths must meet, local municipalities also typically have a say on their allowable use. Cities, counties, and towns may have specific rules on:
- Requiring permits or inspections for temporary paint booths.
- Restricting locations inflatable booths can be set up, especially in residential areas.
- Limiting hours of operation such as prohibiting use at night or on Sundays.
- Requiring notification of neighbors about planned paint booth use.
- Noise limits that apply to exhaust fans and equipment.
- Allowable durations that temporary booths can be erected. 180 days is typical max.
- Proper disposal of used tarps, filters, and other hazardous materials.
- No release of nuisance odors or fumes beyond property lines.
It’s important to thoroughly check local regulations before operating any inflatable paint booth to avoid fines or citations. Getting temporary use permits, notifying fire officials, and learning noise and nuisance rules are key steps for legal compliance.
State-by-State Requirements
Most states follow the national OSHA, NFPA, EPA, and local regulations already covered. However, some states have additional requirements on temporary paint booth facilities that must be followed:
- California – South Coast Air Quality Management District Rule 1151 controls VOC emissions and permitting.
- Colorado – Requires all paint operations register with the Colorado Department of Public Health and Environment.
- Massachusetts – Requires annual registration of paint spray booths with the Office of Public Safety.
- Oregon – Has strict permitting and registration governed by Oregon Revised Statutes 468A.055 – 468A.070.
- Texas – Texas Commission on Environmental Quality (TCEQ) regulates air permits.
- New Jersey – The NJ Department of Environmental Protection manages permitting for temporary booths.
- Pennsylvania – Allegheny County Health Department has additional rules on paint and spray booth VOC emissions.
Some counties or cities within states may also have extra requirements beyond state-level regulations. Always researching the specific location is advised.
Are DIY Inflatable Paint Booths Legal?
The growing popularity of inflatable paint booths has led some hobbyists to try constructing their own DIY versions. This raises questions around whether homebuilt booths meet legal codes.
The short answer is DIY inflatable paint booths are not likely to meet regulations. Building a compliant booth requires:
- Use of properly tested fire-retardant vinyl materials.
- Inclusion of explosion-proof electrical wiring and lighting.
- Precision construction of exhaust ducting to achieve proper air velocities.
- Correct sizing and selection of exhaust fans.
- Proper filtering systems to capture overspray, VOCs, and HAPs.
- Integrating fire suppression systems.
- Documentation and testing of the booth to certify OSHA, NFPA, and EPA compliance.
For all these reasons, it is extremely difficult for homemade paint booths to meet the full scope of legal codes and standards. Violating any requirements puts users at risk of fires, explosions, fines, or other penalties.
Purchasing an inflatable paint booth from a certified supplier is the best way to ensure you receive a booth that meets all applicable regulations right out of the box. Reputable vendors will provide documentation of compliance testing.
If constructing a DIY booth, extreme care must be taken to fully research and implement all local, state, OSHA, NFPA, and EPA requirements. Any modifications to a compliant booth’s systems could also void its approved status.
It is always best to check with local officials before attempting to build or install any spray painting enclosure to understand all legal obligations in your region. Most municipalities prohibit makeshift paint booths that cannot prove compliance.
Using a professional inflatable paint booth is the safest option for staying on the right side of regulations and protecting yourself, employees, and property from serious paint booth risks.
Do Inflatable Paint Booths Need to Be Explosion Proof?
A common question around inflatable paint booth safety is whether they need to be fully explosion proof. With significant amounts of flammable paint chemicals in use, the risk of vapors igniting is a major concern.
Here are the key factors regarding explosion proofing:
- OSHA does require certain electrical components of paint booths to be explosion proof – this includes lighting, wiring, switches, and any other source of sparks. NFPA 33 also mandates explosion proofing.
- Explosion proofing means electrical systems will NOT ignite flammable vapors during normal operation. They are fully enclosed in protective housings.
- Fans and motors also need protective housings and air purging systems to prevent sparking.
- Control panels and devices must also be explosion proof or located outside the booth away from vapors.
- Inflatable booth materials themselves are generally NOT required to be fully explosion proof. Fire-retardant vinyls that don’t readily ignite are acceptable.
- Proper ventilation and airflow prevents buildup of flammable concentrations that could lead to explosion hazard.
Certain components of inflatable booths like lighting and electrical gear need to meet explosion proofing requirements, but the booth structure itself is not required to withstand blasts. Approved fire-retardant materials are sufficient protection. Proper ventilation and following codes limits the overall risk of dangerous paint vapor ignitions.
Reputable inflatable paint booth suppliers ensure all required explosion proof components are integrated to provide a safe system meeting OSHA and NFPA rules. DIY booths likely do not meet all requirements.
Is Heating Allowed in Inflatable Paint Booths?
Maintaining proper painting conditions inside inflatable booths often requires some method of heating. Ambient and surface temperatures impact paint drying and curing processes. Is adding heaters to an inflatable paint booth allowed?
There are specific safety precautions and equipment required when integrating heating systems:
- All heaters must meet NFPA and NEC standards for hazardous location equipment in paint booth environments.
- Natural gas or propane fired heaters are NOT permitted inside booths. Only electric or indirect-fired, ducted heating units are approved.
- Ducted air rotation heaters that distribute heated air through hoses are a common compliant option.
- Heater wiring must be explosion proof and properly grounded.
- Sufficient exhaust ventilation must be in place to prevent flammable vapor buildup.
- Proper minimum clearances around heat sources must be maintained from spray operations.
- Direct-fired make-up air units with long duct runs to isolate heat from the booth interior can also be used.
- Infrared or radiant heating panels require sufficient isolation distances to prevent igniting fumes.
- Thermostat temperature controls are required to prevent overheating.
With the right specialized equipment and careful setup following codes, heating inflatable paint booths is typically allowed. This provides the ability to fine tune painting conditions. Proceed cautiously and consult local officials if unsure.
What Are the OSHA Requirements for Paint Booth Ventilation?
Proper ventilation is one of the most crucial requirements in paint booth systems for safe operation. OSHA sets legal standards for minimum airflow velocities and turnover rates that must be maintained.
The key OSHA requirements for paint booth ventilation under 29 CFR 1910.107 include:
- 100 feet per minute (fpm) minimum exhaust velocity maintained across all booth openings.
- Airflow must direct contaminants away from workers while spraying.
- Total air volume exchange must be between 30-60 air changes per hour.
- Fresh air intakes must have filtration systems to trap overspray.
- Exhaust ducts must vent to a safe point discharge outside.
- All filters must be regularly inspected and maintained.
- Booth air balance should have slightly negative pressure to contain overspray.
- Prevent any air recirculation back into the booth interior space.
- Fans must be properly sized and designed for flammable vapor environments.
- Operators must monitor ventilation effectiveness using instruments like manometers.
- If ventilation becomes ineffective, spray processes must halt until fixed.
Documenting regular testing of inflatable paint booth ventilation speeds and air changes ensures OSHA compliance and helps prevent serious safety hazards from developing.
What Are the Key NFPA Fire Safety Rules for Paint Booths?
The NFPA provides crucial standards on fire hazards and prevention methods specific to paint booth facilities. Here are some of the top NFPA fire safety rules:
- Class I Division I electrical rating required for all permanently mounted booth equipment.
- Grounding of equipment, personnel, and objects being painted is mandated.
- All wiring must meet NFPA 70 electrical code requirements.
- Extinguishing systems must be in place such as sprinklers or portable extinguishers.
- Minimum distances specified between spray operations and other equipment like heaters.
- Accumulation of deposits or residue that could contribute to fire hazards is prohibited.
- Smoking is banned inside or around paint booths.
- Fire alarms, shut-off valves, and emergency exit signage required.
- All participants must receive training on fire prevention procedures.
- No storage of flammable liquids or other combustibles in booth areas.
- Fresh air intakes must prevent spark transfer into the booth interior.
- Documentation of routine inspections and testing of fire-related components.
Careful compliance with all NFPA standards is crucial for limiting the considerable risks of paint booth fires that can result in severe property damage and bodily harm without proper precautions.
Best Practices for Legal and Safe Inflatable Paint Booth Operation
Operating an inflatable paint booth in full compliance with codes and safely requires great attention to detail. Here is a quick checklist covering the most crucial best practices:
- Purchase a booth from a reputable supplier that provides documentation of NFPA, OSHA, EPA compliance.
- Fully research all local and state-level ordinances and acquire needed permits.
- Never modify or disable any safety systems or settings on the booth.
- Routinely test and document ventilation speeds and air changes per hour.
- Inspect all explosion proof electrical components and check grounding wires.
- Keep fire extinguishers nearby and train all users on emergency procedures.
- Properly maintain all exhaust filters and keep replacement filters stocked.
- Monitor noise, odor, and nuisance issues to avoid upsetting neighbors.
- Never use any ignition source in or near the booth when flammable vapors are present.
- Post hazard warning signs and enforce no smoking policies.
- Carefully follow all codes for safe integration of heating systems if needed.
- Keep flammables like paint solvents properly stored outside the booth interior.
Staying up to date on all regulations and implementing best practice guidelines is key to safe, compliant, and legal operation of any inflatable paint booth system. Consult local authorities if ever unsure about proper procedures. With prudent operation, inflatable paint booths can offer a flexible solution for spray finishing needs across diverse industries and use cases.